The Consulting Group 2006 Ltd
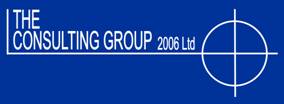
Greg Shaw | |
325 Hibiscus Coast Highway Orewa Auckland 0931 |
Phone: 0274 955 250 |
Email: |
A History
Greg Shaw has been involved in Civil, Structural and Marine Engineering, since 1976. He is a recognized expert in New Zealand in the field of foreshore marine engineering and as such, acts on behalf of the Government’s Minister of Conservation, on Planning, Engineering and Conservation matters, for proposed Marine Projects. He is 1 of only 14 such persons.
In 1979, he was the Marine Division Manager, for the design and construction of the major extension to Westhaven Marina, Auckland, New Zealand.
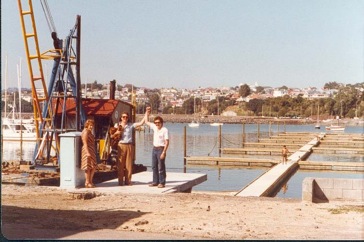
1980, First Walkway Section Completed, Westhaven
This was the FIRST marina in New Zealand to adopt the “Polystyrene and Concrete” concept, that is widely used today. Greg not only designed the entire system, but he designed the casting moulds for the floatation units, established the precast factory and supervised the assembly of the units on the water and the entire construction process. This was a unique experience, to be knowledgeable of all aspects of the project, from start to finish.
This marina remains the focal point of the Marine Scene in Auckland and is functioning as designed, some 28 years after construction.
In 1981, Greg sought experience offshore and took up a position with one of the world’s largest engineering companies, Bechtel, as Senior Construction Engineer on a $150 million Port Development Project in Jubail, Saudi Arabia. This project allowed Greg to learn about large scale dredging work, large scale rock wave protection structures and specialized wave protection devices, known as “Stabits”. These are large precast concrete tetrapoidal interlocking units, which can be used when there is a shortage of suitable large rocks.
Management skills developed further were :- Scheduling and programming, material tracking systems, quality control systems.
Since 1988, Greg has continued to be involved with general Marine Projects, designing fendering systems for Auckland wharves and currently he is working on the upgrading of a wharf on Niue island in the South Pacific, including a study of a proposed marina facility. His continued involvement in Marina Design has initiated many refinements, since the first designs, of 28 years ago.
Marine Engineering Today
Today’s marinas have many improved features. A few of the obvious ones are :-
- Wider main walkways.
- Longer “Unit” lengths, hence less joints.
- Use of artificial timbers in part, provides more uniform stiffness.
- Covers for the Tie rods, to lessen corrosion.
- Longer “finger” units, giving greater strength to side impact loads.
- Improved “knee” joints, between fingers and walkways.
- “Smart Card” operated and metered access gates, power and water supplies, and beverages.
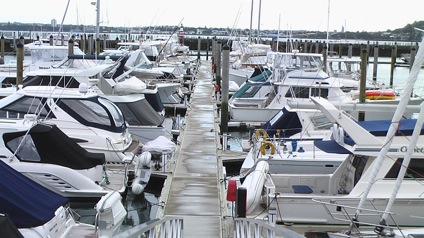
Most Recent Marina Design, Auckland, New Zealand
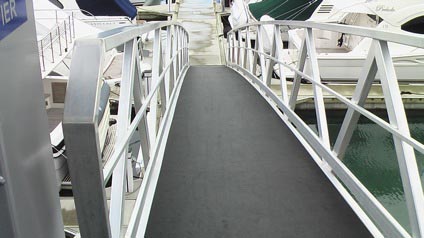
New, Curved, Aesthetically Pleasing, All-Aluminium Gangway
Our designs consists of safe, permanent, environmentally friendly concrete modules requiring minimal maintenance, offering impressive durability in a variety of configurations and appearances to keep individual projects looking distinctive.
There are now over 6,000 such style of berth in New Zealand, which is a very high number in proportion to our population.
Service Offered By The Consulting Group 2006 Ltd
Our aim :-
“TO WORK IN PARTNERSHIP WITH OUR CLIENTS, TO ENSURE THAT THEY OBTAIN THE MOST COST EFFECTIVE, WORLD CLASS MARINA FACILITY POSSIBLE.”
Concept Plans
Our specialist designer will liaise with the client, to determine the best solution to the proposed marina. Analysis of berthing ratios will be carried out, along with the need for specific infrastructure. For example, what onshore facilities are required? Is there a need for a Travel Lift? Hardstand area for boat servicing, car parking, repair services, retail shops, yacht clubs, restaurants, cafes, accommodation, laundry, showers and toilets, boat launching ramps etc…
A typical concept plan includes for example:
- 200 Berths ranging in size from 10.5 – 20m
- 2 Large car parks (located each end of Marina)
- Boat Broker/Dealership
- Hard stand and maintenance area to cater for up to 12 boats
- Haul out area
- 35 tonne travel lift
- Boat repair facilities
- Small workshops for associated marine servicing businesses
- Dry stack storage for 60 boats
- Environmentally friendly boat cleaning/wash down facilities
- Modern ablution/shower/laundry block
- Café/Shop and restaurant
- Boating Club
- Chandlery shop
- An onsite management office to oversee the operational running of the marina including dredging to control silt build-up, site security and to co-ordinate the lease and re-sale of berths
- Accommodation and apartments
- Breakwaters and wave protection structures
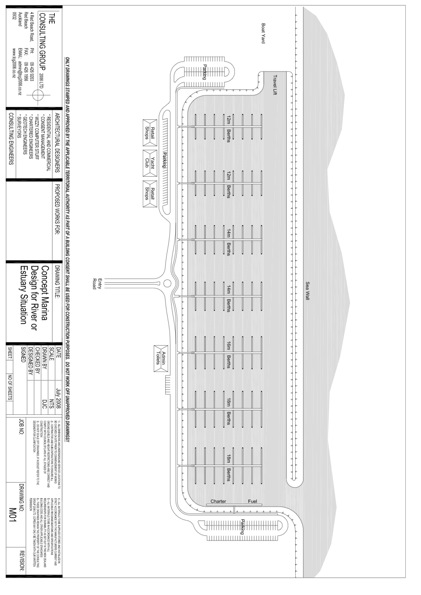
Sample Marina Design for River or Estuary Situation
Final Engineering Design and Design Plans
Once we are provided with full wave climate data, wind design data, tidal data, river current data, flood event data, cyclone data, sea bed depth and sea bed geotechnical data, precise engineering structural design can be completed.
The wave protection structure is one of the key elements to be designed, to ensure that the wave climate within the marina itself is kept to no greater than 300 mm wave height. The foundations of the structure will have to be fully understood and designed to accommodate whatever sea bed conditions exist.
Next will be the pile design, as these are required to resist all the wind loadings. Depending upon wind speed design and water depth and sea bed conditions, the piles will be either steel or precast reinforced concrete.
The Concept Plans are next developed into full working design drawings. Depending upon the interface with the main developer’s architect, they may include the immediate foreshore area, parking, hard stand, boat servicing areas, dry stack marina, boat club, restaurants, retail shops, boat haul out areas, fuel jetty, wash down facilities, pump out of effluent facilities etc.
Detailed layout of the marina itself would be shown, along with all facilities such as water, power, lighting, gangways, security gates and the like.
Details of the dredging requirements and rock break waters and sub seas works would be detailed, if not covered by the main project consultants.
There are shop drawings required for each precast unit, which is then numbered and detailed, to allow for it’s special requirements, such as longitudinal ducting, cross ducting, access boxes etc.
Quantity Surveys
If required, we can assist with a quantity survey of the entire marina construction process, in order to determine the Budgeted Project Cost. This will be a very useful service when the client is also the developer of the marina and will be undertaking the manufacture of the units and on site construction, themselves.
A quantity analysis will rapidly allow cost estimates to be done for the project, in order to compare the cost of “self build”, compared with importing a “kitset marina from another country”.
There is guaranteed to be significant financial benefit, by building the marina yourselves, utilizing our companies assistance.
Pre-cast Factory Establishment
Our business model is based upon the client manufacturing the marina units themselves ( by sub contract) under the guidance of The Consulting Group 2006 Ltd. (TCG)
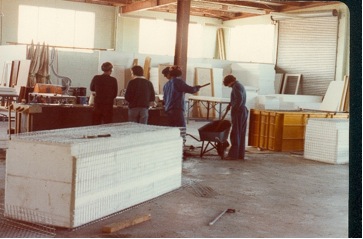
Inside The Precast Factory
The client will need to locate a suitable precast manufacturing factory, within easy transport options of the proposed project. TCG will provide detailed designs for the required concrete moulds. Alternately, these moulds can be manufactured in New Zealand and shipped to the precast factory.
TCG would provide detailed designs of the polystyrene core block shapes, ducting and the like, detailed design of the reinforcing requirements etc. Units will be manufactured under License to TCG.
TCG would provide expertise in the construction supervision of the manufacture of the precast units, thereby ensuring the highest quality product.
Project Management
TCG can supply an expert Construction Manager, to oversee the on site installation of the precast units. They would assist with supervision of the entire assembly, the installation of services, piling, dredging, break water construction, as required.
There would be liaison between the sub contractors and the main contractor and the client’s requirements. This would ensure that the timelines are maintained and that the Project Milestones are reached.
Post Construction Services
We can assist with management policies and procedures for effectively running and managing the Marina facility, once it is completed. We can supply specially developed software, to aid in this process.
The use of new “smart cards” can aid the process of marina management, as costs associated with each user are clearly defined. The “smart card” not only allows entry through the security gates, but can also be used to allocate costs associated with power usage, water usage and even used for the purchase of food and beverages at the Yacht Club. It may also possibly allow access to the ablution facility and laundry services, for visiting Boaties.
Management software will be required to allocate annual berth fees, keep track of short term rental fees and also the sale and re-purchase of berths.